GreenTech Fuels – Operation and Maintenance (O&M) Details
At GreenTech Fuels, we understand the importance of ensuring the consistent and efficient operation of our energy generation systems, which include biomass gasifiers, waste-to-energy plants, syngas generators, and more. To maximize the lifespan, performance, and sustainability of our systems, we offer comprehensive Operation and Maintenance (O&M) services. Our O&M solutions are designed to ensure that our installations continue to operate at peak efficiency while minimizing downtime, reducing operational costs, and optimizing energy output.
1. Operation and Maintenance Services Overview
GreenTech Fuels provides an integrated O&M service package that includes monitoring, servicing, troubleshooting, and optimizing all aspects of our renewable energy systems. Our goal is to ensure that our systems run smoothly, with minimal interruptions, maximizing both financial and environmental benefits for our clients.
2. Key Components of O&M Services
a. Preventive Maintenance
Regular preventive maintenance is essential to the longevity and efficiency of the energy systems. Our team follows a strict schedule of maintenance tasks to minimize wear and tear on the equipment. This includes:
Routine checks and diagnostics on mechanical, electrical, and control systems.
Cleaning of key components like filters, gasifiers, and boilers to maintain optimal performance.
Ensuring proper calibration and adjustments to keep the system running at peak efficiency.
Replacing worn-out components proactively to prevent breakdowns and optimize system output.
b. Corrective Maintenance
Our team is equipped to handle unexpected breakdowns or failures. The corrective maintenance process includes:
Rapid response to unplanned issues, ensuring minimal downtime.
Diagnosis and resolution of technical issues or malfunctions in the system.
Repairing or replacing damaged components such as gasifiers, turbines, and generators.
Ensuring compliance with safety standards and environmental regulations during repairs.
c. System Monitoring and Performance Analysis
Through advanced monitoring tools, we continuously track the performance of each energy system:
Remote monitoring of key performance indicators (KPIs) like energy output, fuel efficiency, and emissions levels.
Performance analysis to identify underperformance issues and recommend corrective actions.
Data-driven insights to predict and prevent potential failures.
Real-time alerts and notifications for system faults or maintenance needs.
d. Fuel Management and Optimization
Efficient fuel management is critical to maximizing the efficiency of our biomass and waste-to-energy systems. Our services include:
Continuous monitoring and optimization of fuel quality and consistency.
Identifying the most cost-effective fuel sources for biomass, waste, or other feedstocks.
Ensuring that fuel is stored and handled properly to prevent contamination or degradation.
Analyzing fuel consumption patterns and adjusting operation to reduce waste and improve efficiency.
e. Equipment Upgrades and Retrofits
As technology advances, we ensure that our systems stay up to date with the latest innovations:
Offering retrofitting services to upgrade older equipment and integrate new technologies for improved performance and energy output.
Implementing cutting-edge systems for waste-to-energy conversion, like advanced gasifiers or more efficient turbines, to reduce costs and increase reliability.
Regularly reviewing the system design and identifying opportunities for improvements to match evolving energy needs and environmental standards.
3. Operational Safety and Compliance
Safety is at the core of our O&M services. Our team adheres to strict safety protocols to ensure that all operations are carried out safely, efficiently, and in compliance with industry standards and regulations:
Regular safety audits and inspections to ensure compliance with local and international safety standards.
Risk assessments and mitigation strategies to handle any potential hazards, such as fire, explosion, or emissions leaks.
Strict adherence to environmental regulations, ensuring that the system operates within acceptable limits for emissions, noise, and waste.
Training programs for operators and staff to ensure they are equipped with the latest safety knowledge and best practices.
4. Customer Support and Training
We believe in providing strong support to our clients, helping them operate their systems efficiently. Our services include:
Operator Training: We provide comprehensive training for client personnel on how to operate, troubleshoot, and maintain the systems.
Technical Support: Our expert technicians are available to provide guidance, resolve issues, and assist with technical inquiries via phone, email, or on-site visits.
Documentation and Reporting: Clients receive detailed performance reports, maintenance logs, and compliance documents to help them track system performance and stay up to date on necessary tasks.
Spare Parts Management: We provide a streamlined process for ordering and delivering spare parts, ensuring that essential components are always available when needed.
5. Environmental Impact Monitoring
As part of our commitment to sustainability, we also monitor the environmental performance of our systems:
Emissions Monitoring: Our O&M services include continuous monitoring of emissions to ensure compliance with environmental regulations and to minimize the environmental footprint.
Waste Management: Ensuring that waste products from the energy generation process are properly handled, treated, and disposed of in an environmentally responsible manner.
Water Usage: Monitoring water usage and ensuring that systems like boilers operate efficiently, reducing water waste and ensuring water is recycled wherever possible.
6. Performance Warranty and Guarantees
To give our clients peace of mind, we provide performance warranties and guarantees:
Performance Guarantees: We guarantee that the system will perform within the agreed-upon parameters for energy output, emissions, and operational efficiency.
Extended Warranties: GreenTech Fuels offers extended warranties for key components, providing coverage beyond the standard warranty period to ensure long-term performance and reliability.
7. Customized O&M Plans
We understand that each project is unique, which is why we offer customizable O&M plans that are tailored to each client’s specific needs. Whether it’s a large-scale biomass plant or a small community-based waste-to-energy project, we create a maintenance plan that fits the scope, technology, and operational goals of the installation.
8. Performance and Cost Optimization
Through our ongoing O&M efforts, we aim to optimize system performance while reducing operational costs. We use the following methods:
Regularly review the system’s efficiency to identify areas for optimization and cost savings.
Implement best practices to reduce energy consumption, fuel costs, and maintenance expenses.
Explore opportunities for energy recovery and additional revenue streams, such as selling excess energy to the grid or utilizing byproducts.
By entrusting GreenTech Fuels with your Operation and Maintenance needs, you can ensure the long-term success and sustainability of your energy generation systems. Our dedicated team of experts is committed to delivering the highest level of service, optimizing energy production, and ensuring the environmental impact is minimized.
For more information on our O&M services, please feel free to contact us.
HOME
ABOUT US
PRODUCTS
PROJECTS
TECHNOLOGY
SOLUTIONS
MEDIA CENTRE
CONTACT US
© 2024. All rights reserved.
PRODUCTS
BIOWATT COMPACT BIOMASS GASIFICATION POWER GENERATION SYSTEM
BIOMASS GASIFICATION POWER PLANT
BIOMASS GASIFIER
BIOMASS CARBONIZER
BIOMASS GASIFIER FOR GREEN-CHEMICAL
BIOMASS GASIFICATION BOILER
BIOMASS CARBONIZATION POWER PLANT
BIOMASS CARBONIZATION BOILER
COAL GASIFICATION POWER PLANT
COAL GASIFIER
WASTE GASIFIER
WASTE GASIFICATION POWER PLANT
SYNGAS GENERATOR SET
PRODUCER GAS GENERATOR SET
BIOMASS GAS GENERATOR SET
COAL GAS GENERATOR SET
GAS PURIFICATION SYSTEM
DECORBONIZATION
GREENTECH SOLAR
NANO HYDROPOWER
GREENTECH BATTERIES
HUSKTECH
CONTACT US
GREENTECH FUELS
GREENTECH HABITAT CENTER
CHOUPARAN, HAZARIBAGH, JHARKHAND, INDIA - 825406
📞 +91 6207423061
📞 +91 9973352599
www.greentechfuels.in
📧 info@greentechfuels.in
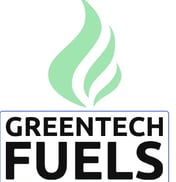
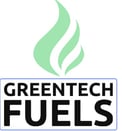