GreenTech Fuels likely utilizes gasification technology as part of its waste-to-energy solutions. Gasification is a thermal conversion process that turns carbon-containing materials such as biomass, municipal solid waste (MSW), and other organic materials into syngas (synthesis gas) through a reaction with limited oxygen or steam. This process can be used to produce electricity, heat, or biofuels, making it an essential technology for renewable energy generation.
Gasifiers come in different types, each suited to specific feedstocks and desired outputs. Below are the main types of gasifiers that may be used by GreenTech Fuels:
1. Fixed Bed Gasifiers (Updraft & Downdraft)
Updraft Gasifier:
Working Principle: In an updraft gasifier, the feedstock is introduced at the top of the gasifier, and the gasification process occurs as the material moves downward through a bed of hot char (carbon residue from the feedstock). The gasification process is initiated by limited oxygen and high temperatures.
Features:
Higher tar content in syngas, which may require additional cleaning.
Typically used for larger-scale systems that process larger particles.
Best For: Biomass feedstocks like wood chips, agricultural residues, and MSW.
Downdraft Gasifier:
Working Principle: The feedstock is introduced at the top of the gasifier, and as it descends, it undergoes gasification while passing through the hot char bed and a zone of controlled oxygen and steam. The syngas is produced at the bottom of the gasifier.
Features:
Lower tar content in the syngas compared to the updraft system, making it more suitable for engines or turbines that use the syngas for power generation.
More efficient and cleaner syngas.
Best For: Smaller, more efficient systems that can handle finer feedstocks like wood chips, rice husks, and other organic materials.
2. Fluidized Bed Gasifiers
Working Principle: A fluidized bed gasifier uses hot sand or another inert material that is kept in motion (fluidized) by a stream of air or steam. The feedstock is introduced into this bed, where it is subjected to high temperatures and partial oxidation. The process produces syngas.
Features:
More uniform temperature distribution compared to fixed-bed systems.
Can handle a wide range of feedstocks, including biomass, coal, MSW, and even plastic waste.
Typically produces cleaner syngas with lower tar levels.
Best For: Medium to large-scale systems, capable of processing various types of feedstock like agricultural waste, MSW, or even coal.
3. Entrained Flow Gasifiers
Working Principle: In an entrained flow gasifier, the feedstock (usually in powdered form) is introduced into a high-temperature, high-pressure stream of oxygen or steam. The particles are "entrained" or suspended in the gas flow, and they react quickly to produce syngas.
Features:
Extremely high temperatures (up to 1,500°C) allow for the rapid conversion of feedstock into syngas.
Highly efficient and capable of producing clean syngas with minimal tar formation.
Typically used for coal, petcoke, and biomass processing.
Best For: Large-scale, high-efficiency applications such as power plants or industrial operations that require a consistent supply of syngas.
4. Plasma Gasifiers
Working Principle: Plasma gasifiers use an electrical arc to generate extremely high temperatures (up to 10,000°C) to convert feedstocks into syngas. The feedstock is introduced into the plasma torch, which breaks down the molecular bonds of the materials and produces clean syngas.
Features:
Extremely high temperatures result in near-complete breakdown of complex organic materials, including plastics and hazardous waste.
High energy consumption in the plasma process, making it less cost-effective than other gasifiers for some applications.
Produces virtually no tar and produces a very clean syngas.
Best For: High-value, specialized applications such as hazardous waste treatment, tire recycling, and converting non-recyclable materials into energy.
5. Biomass Gasifiers
Working Principle: Biomass gasifiers are specifically designed for processing organic materials such as wood chips, agricultural residues, and food waste. These gasifiers use a limited amount of air or steam to convert the biomass into syngas (a mixture of hydrogen, carbon monoxide, and methane).
Features:
High flexibility in feedstock type and size.
Typically employed in both small and medium-scale energy projects.
Can produce electricity or biofuels from biomass.
Best For: Localized applications like community-scale power generation, rural electrification, and biofuel production.
6. Oxygen-Enhanced Gasifiers
Working Principle: These gasifiers use pure oxygen or oxygen-enriched air instead of regular air, which helps achieve higher temperatures and increases the efficiency of the gasification process.
Features:
Higher efficiency and cleaner syngas output.
More compact than air-based systems and can achieve quicker start-up times.
Typically used for smaller feedstock or where high purity of syngas is required.
Best For: Industrial and commercial-scale projects that require efficient gasification with high purity syngas.
Comparison of Gasifier Types:
Gasifier TypeFeaturesBest ForEfficiency/OutputUpdraft GasifierSimple, suitable for larger particlesBiomass, MSWModerateDowndraft GasifierCleaner syngas, efficient for small-scale useSmall to medium biomass (wood, rice husks)HighFluidized Bed GasifierUniform heat, flexible feedstock handlingBiomass, MSW, coalHighEntrained Flow GasifierHigh efficiency, minimal tarLarge-scale power generationVery HighPlasma GasifierVery high temperatures, clean syngasHazardous waste, plastic recyclingVery HighBiomass GasifierTailored for organic wasteCommunity power, biofuel productionModerate to HighOxygen-Enhanced GasifierOxygen for higher efficiency and cleaner outputIndustrial applicationsHigh
GreenTech Fuels likely uses the most appropriate type of gasifier based on the waste materials available, the scale of the operation, and the desired output. Whether the goal is to convert biomass into biofuels, treat municipal solid waste, or create clean syngas for power generation, choosing the right gasifier ensures optimal performance, minimal environmental impact, and cost-effectiveness.
HOME
ABOUT US
PRODUCTS
PROJECTS
TECHNOLOGY
SOLUTIONS
MEDIA CENTRE
CONTACT US
© 2024. All rights reserved.
PRODUCTS
BIOWATT COMPACT BIOMASS GASIFICATION POWER GENERATION SYSTEM
BIOMASS GASIFICATION POWER PLANT
BIOMASS GASIFIER
BIOMASS CARBONIZER
BIOMASS GASIFIER FOR GREEN-CHEMICAL
BIOMASS GASIFICATION BOILER
BIOMASS CARBONIZATION POWER PLANT
BIOMASS CARBONIZATION BOILER
COAL GASIFICATION POWER PLANT
COAL GASIFIER
WASTE GASIFIER
WASTE GASIFICATION POWER PLANT
SYNGAS GENERATOR SET
PRODUCER GAS GENERATOR SET
BIOMASS GAS GENERATOR SET
COAL GAS GENERATOR SET
GAS PURIFICATION SYSTEM
DECORBONIZATION
GREENTECH SOLAR
NANO HYDROPOWER
GREENTECH BATTERIES
HUSKTECH
CONTACT US
GREENTECH FUELS
GREENTECH HABITAT CENTER
CHOUPARAN, HAZARIBAGH, JHARKHAND, INDIA - 825406
📞 +91 6207423061
📞 +91 9973352599
www.greentechfuels.in
📧 info@greentechfuels.in
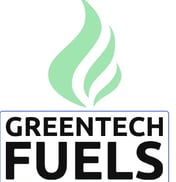
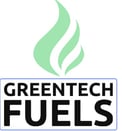